Risks of Ignition
There are four elements to examine in order to understand the risk of an ignition of sensitive flammable gas, vapor and dust atmospheres. performance
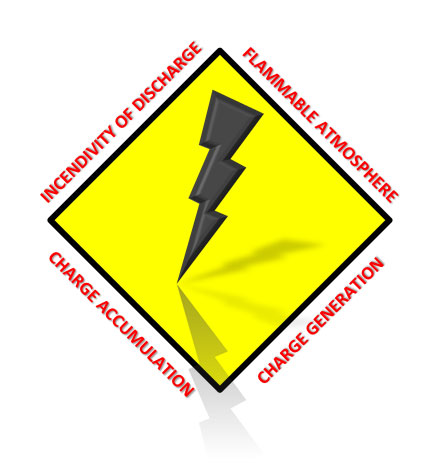
The first element is the sensitivity of the surrounding flammable atmosphere, i.e., how easily is the gas, vapor or dust atmosphere ignited. The sensitivity is measured by the minimum ignition energy (MIE) of the flammable atmosphere. The ignition energy varies depending of the mixture of the flammable gas, vapor, or dust and air or oxygen so the minimum is used to ensure worst case. Typical MIEs for flammable vapor atmospheres found in industry range from 0.14mJ to 0.25mJ.
- Minimum Ignition Energy
- Hydrogen - 0.01mJ
- Ethylene - 0.07mJ
- Methanol - 0.14mJ
- Ethane - 0.24mJ
- Propane - 0.25mJ
The second element is charge generation. Charge is generated in an industrial setting by triboelectrification or tribocharging. Triboelectrification occurs when materials separate from each other. During the filling or emptying of FIBCs this can occur in a number of ways
- Particles or pellets of product contacting and separating from each other
- Product contacting and separating from the surfaces of conveying equipment
- Product contacting and separating from the FIBC surfaces
The third element is charge accumulation. In the presence of triboelectrification, charge will accumulate on any isolated surface whether these surfaces are of conductive, dissipative or non-conductive materials. Conductive materials have volume resistivity of less than 104 Ω. Dissipative materials have volume resistivity of greater than 104 Ω and less than 109 Ω. Non-conductive materials have volume resistivity greater than 109 Ω. Most plastic materials including the FIBC polypropylene woven fabric are non-conductive. In evaluating performance the rate of charge flowing into an FIBC or the charging current is used to characterize the how much charge is accumulating during a period of time. Leading experts from around the world have established 3 µ A is an appropriate safe maximum value for charging rate for industrial applications involving FIBCs.
The fourth element is the incendivity of the discharge. The incendivity depends on the mechanism for the discharge of accumulated charge. There are five mechanisms or types of discharges.
Spark | Spark discharges occur between two conductors and has energy of up to several joules. These discharges can and do occur in Type A FIBC and TYPE B FIBC and in Type C FIBCs that are not properly grounded. The more conductive the network within the groundable Type C FIBC is the more energetic the spark discharge may be. |
Propagating Brush | Propagating brush discharges occur between an insulator and conductor. These discharges can have energies of several joules and are avoided in FIBCs by using fabric with breakdown voltage of less than 6kV. |
Brush | Brush discharges occur between an insulator and a conductor but is much less energetic at around 4mJ but still sufficient to ignite sensitive atmospheres. These discharges are a major concern in groundable Type C FIBCs and led to the stringent spacing requirements for the conductive networks. |
Cone | Cone discharges may occur during the filling process. The accumulation of product causes a compaction of the product below which can release a cone discharge. |
Corona | Corona discharges occur when the air surrounding the charge breaks down and is ionized. These discharges are very low energy and are believed to be capable of igniting only hydrogen. |